BMW has been forced to suspend production of the Mini for the second time in 12 months with the German brand citing a shortage of computer chips for the stoppage. Although production is expected to restart on Saturday (26 February), the knock-on effect in terms of delayed orders and deliveries from other suppliers to the plant is significant. Around 3,500 workers are based at Oxford which normally produces about 5,000 cars a week.
In a statement BMW said: "As a result of the global semiconductor shortage, an issue that has affected the entire automotive industry for the last year, Plant Oxford is making some short-term adjustments to its production schedule.Plant Oxford is standing down five days of production - Monday 21 February to Friday 25 February inclusive, for all shifts. We are monitoring the situation very closely and are in constant communication with our associates and suppliers."
The news comes as the entire car business battles with a crippling lack of semi-conductors (microchips). Earlier this week, Volkswagen adjusted its entire ID.3 range in an effort to streamline production at its factory in Germany. Customers are currently only able to order ID.3 models in Life trim, which has the lowest level of standard equipment. The brand plans to reinstate higher spec models as the shortage eases.
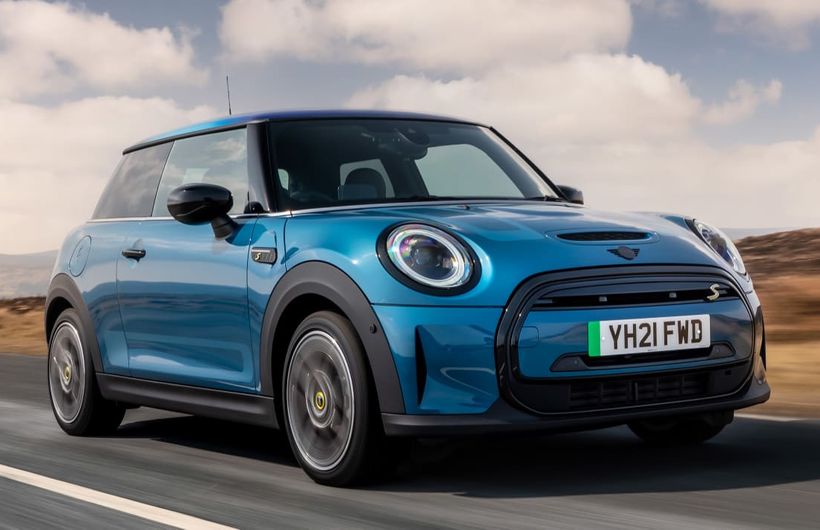